Low temperatures experienced during winter months can increase the risk of damage to property and injury to personnel and consequent costly claims, and it requires specific consideration when managing the risks of a business.
Prevention of Freezing Water Systems
There are a number of practical steps that can be taken to protect businesses against water damage caused by bursting pipes and other water/fluid-charged apparatus.
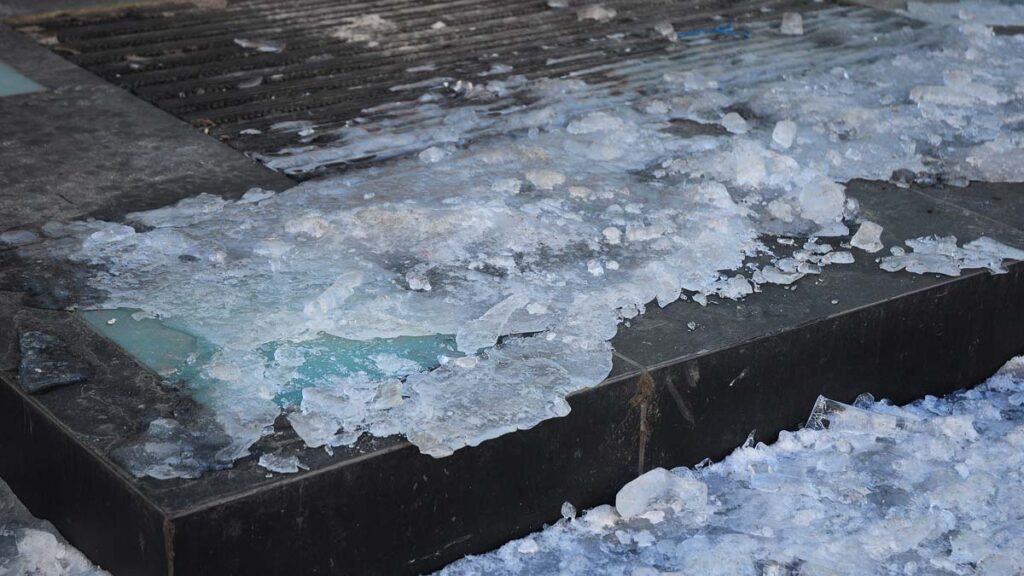
- Lag pipes to delay the temperature drop. Using at least 25mm thick, good quality, noncombustible lagging, securely fixed to all piping, including bends and expansion pipes.
- Lag around and over tanks, but not underneath so that heat from below can reach them.
- Lagging cannot solely be relied upon to prevent freezing in sustained subzero temperatures, if possible, the following sources of heat should be considered:
- Generalised heat in the building (essential where pipe work is extensive).
- Trace heating (electrical heating tapes wrapped around pipes) with lagging over.
- Immersion heaters within storage tanks.
- Install low-temperature sensors (frost-stats) designed to override normal heating controls to activate heating systems when temperatures fall below 4oC.
- Maintain adequate heating over extended holiday/closure periods.
- Minimise pipe-runs outside, or in areas exposed to winds, and make sure they are adequately protected.
- Where systems are disused, or premises are unoccupied water systems should be drained down and isolated.
Minimising Damage at Your Premises
- Store stock, which is valuable or liable to water damage, and locate sensitive areas such as computer suites, away from water storage tanks and fluid-carrying pipework.
- Keep stock off the floor (use of stillages and racking).
- Provide catch trays for tanks with drainage to a safe location.
- The premises should be regularly visited (ideally daily but at least twice weekly) during shutdowns or periods of unoccupancy, to make sure precautions are effective.
- Installation of proprietary automatic control valves activated by water-flow detectors to automatically cut off the water supply in the event of prolonged water flow following a burst.
The following measures should be taken if pipes are found to be frozen.
- Isolate the affected pipe by closing the stopcock or feed from the mains or tank.
- Anticipate leakage and protect wiring, machinery or stock in the immediate vicinity.
- Open the tap nearest to the frozen section.
- Use a gradual heat source such as hot water bottles or a hairdryer against the pipe, or raise the temperature of surrounding air by space heating.
- Do apply heat by blowlamp or hot air paint stripper as sudden heating may cause the pipes to burst. Never use a naked flame.
Managing Sprinkler Installations
Where premises are protected by automatic sprinkler systems, special consideration is needed. Whilst sprinkler systems are designed and installed to meet the specific demands of a particular trade and occupancy, circumstances can change which increase the risk of sprinkler pipes freezing.
Where the temperature within a premises cannot always be maintained above 5oC, the risk of water in sprinkler range pipes freezing increases and therefore “dry” or “alternate” systems are installed, which are charged with air, either permanently (dry), or during winter months (alternate). It must be ensured that system design is appropriate to current use and heating arrangements.
Sections of the sprinkler system, which are exposed to the elements, such as loading canopies, should be protected with electrical trace wire heating and lagging to prevent freezing. Alternatively, these parts (so called “tail ends”) of the system should be drained and filled with air.
Liability Exposures
The presence of ice and snow can introduce new hazards to staff and visitors attending a premises or going about their normal work activities. The following will help reduce the risk of injury:
- Ensuring that the respective risk assessments include relevant risk controls for winter weather. These should be regularly reviewed and communicated to all parties effected.
- Having a suitable salting/gritting procedure together with policies to ensure that they are implemented when required.
- Assessing the suitability of site transport vehicles for safe use in such conditions.
- Providing suitable thermal clothing and appropriate anti-slip footwear for employees working in cold conditions.
- Assessing the risk of slips on access platforms and, if necessary, suspend any work at height.
- Introducing emergency procedures and guidance on safety in extreme conditions whilst driving at work.
- Completion of maintenance work and repairs, in response to emergency situations or damage, must be risk assessed to take account of adverse weather.
- Slippery paths can result in claims being brought under the Occupiers Liability Act which obliges the owner or occupier of private land to ensure safe access for visitors. The HSE offers extensive guidance which references not only ice and snow, but also wet and decaying leaves.
For more information on how you can get your business protected from a risk management perspective, please speak to your licensed insurance brokers, who will be able to provide a risk management solution from Arch.*
*Available to eligible commercial policyholders.