Spark erosion machining — also known as electrical discharge machining (EDM) and, in its conventional form, die sinking — is commonly used in engineering to produce highly accurate dies and moulds with complex geometries.
Spark erosion is a known source of major fires in engineering premises. These commonly occur when a flammable dielectric fluid reaches its flashpoint in the presence of a spark and adequate supply of air.
Control Measures
Spark erosion machines should be installed, operated and maintained in accordance with the manufacturer’s instructions. Particular attention is needed to ensure that safety devices and, where fitted, fire suppression systems are maintained in full working order. This is best done under a formal planned preventative maintenance programme.
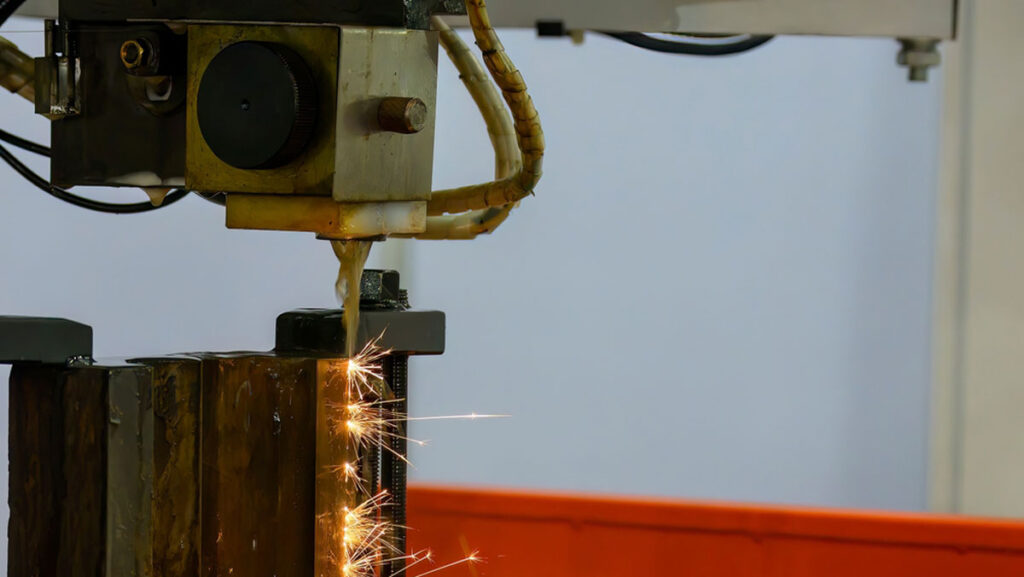
Spark eroders should be positioned away from combustible items and materials, including building materials and linings and where practicable — particularly if used unattended out-of-hours — within an enclosed area of the premises having a minimum fire resistance of 60 minutes.
Employees should be suitably trained in the correct operation of spark eroders and associated hazards, which include the risk of injury or death from high voltage electricity.
A dielectric with the highest flashpoint practicable should be specified. The working temperature of the fluid should be at least 30°C below the auto ignition temperature of the fluid. A number of safety devices can be fitted to spark eroders in order to reduce risks:
- Both electrodes should be fully immersed below the surface of the dielectric fluid. A fluid level control device (commonly a float switch) should be installed to shut the machine off before the fluid level becomes critically low. For additional safety, two switches are recommended.
- A thermostat should be incorporated to stop the process should the temperature of the dielectric fluid rise above a predetermined level. This should set be at least 10°C below the flashpoint of the fluid. For additional safety, two thermostats are recommended.
- Larger machines may use water cooling to prevent the dielectric from overheating.
- An electrode immersion (back-off) switch will automatically shut the machine down if the electrode retracts a preset distance due to debris between the die and workpiece.
- Anti-arc control detects arcing caused by waste or a broken electrode tip, retracts the electrode to enable flushing by the dielectric and shuts the machine down if this is unsuccessful.
- Fixed start point monitoring shuts the machine down should the electrode retract above its starting point. This is independent of the back-off switch.
Not all of the above devices may be present on some machines, particularly older models. It may however be possible to retrofit these following consultation with the machine manufacturer or other specialist.
Unattended Operation
Spark erosion machining is a slow process and machines are typically left to operate with minimal supervision or completely unattended for extended periods of time, sometimes overnight. In these circumstances, any fire originating within the machine could develop undetected, with potentially catastrophic results.
Modern spark eroders with pulse monitoring and correction functions, which optimise the spark gap and electrical conditions, are designed to work with minimal supervision. Machines without these controls should not be run unattended.
Spark eroders which operate unattended out-of-hours should always be fitted with automatic fire suppression using a suitable extinguishant (this can be determined by reference to the material safety data sheet for the dielectric fluid).
Fire suppression systems used with spark eroders are commonly activated by infrared flame (preferred) or heat (bulb, fuse, trace tube or other) detector and should be configured to shut the machine down upon activation and generate a ‘fire’ signal to an approved alarm receiving centre, initiating fire brigade and keyholder attendance. This is commonly done via a remotely monitored automatic fire alarm system.
The fire suppression system should be inspected, tested and maintained in accordance with any recommendations made by the manufacturer and installer.
For more information on how you can get your business protected from a risk management perspective, please speak to your licensed insurance brokers, who will be able to provide a risk management solution from Arch.*
*Available to eligible commercial policyholders.