Introduction
Glassfibre is a composite material often referred to as Glass Reinforced Plastic (GRP) and can also be known as Fibre Reinforced Plastic (FRP).
GRP is composed of strands of glass woven into a flexible fabric. The fabric is normally placed into a mould and built up in a lamination process with resin which after curing results in a product with a high strength-to-weight ratio, making it useful for products such as water tanks, boat hulls, architectural features and vehicle body panels.
Two of the most common open mould methods of GRP production are hand lay-up and spray lay-up, less common GRP moulding processes use similar or the same materials presenting similar hazards.
Hand Lay-Up
Hand lay-up is the simplest, cheapest and oldest open moulding method of the composite fabrication processes. It is a low-volume, labour-intensive method suited especially for simple shapes, such as boat hulls, structural coverings, baths and the like. Gel coat is then poured, brushed or sprayed over or into the mould, forming the outer coating of the product. Layers of woven glass fibre matting impregnated with polyester resin and catalysts are then placed over the gel coat with any entrapped air being removed manually. A catalyst is added to the polyester resin immediately prior to the lamination process to start the curing process. The catalyst is usually an organic peroxide such as Methyl Ethyl Ketone Peroxide. Once hardened/cured the product is removed from the mould and is trimmed usually by air driven hand tools.
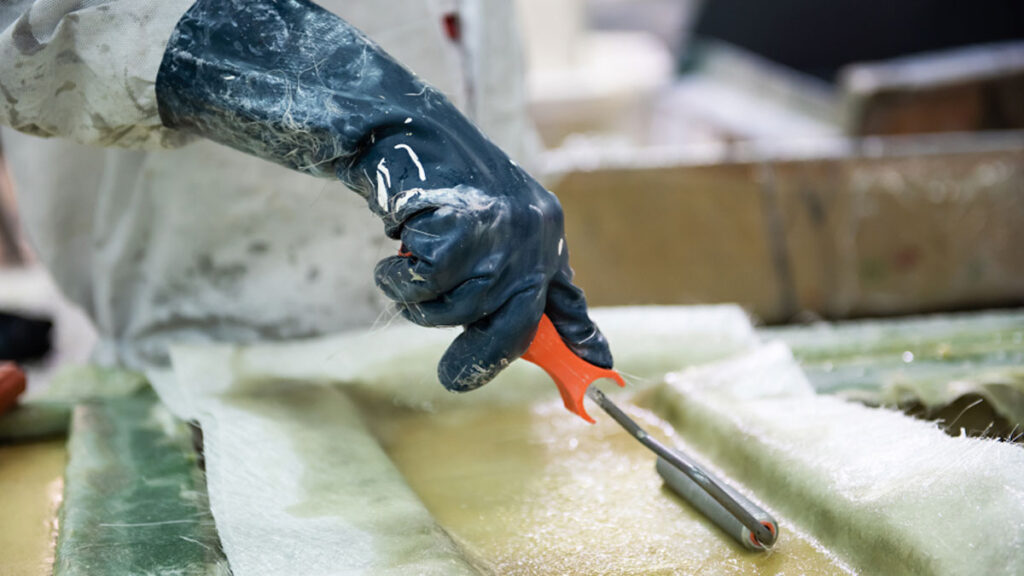
Spray Lay-Up
This is the same principle as hand lay-up, however the laminating process changes after the gel coat is applied. This technique is usually used for larger projects/products such as water tanks, caravan body panels and swimming pools. A spray gun applies the resin, catalyst and matting to the mould, the resin and catalyst are mixed at the spray nozzle and the matting is chopped into small strands which are carried onto the mould in the resin stream. Once cured, it is removed from the mould and trimmed as with the hand lay-up process. The spray gun system is also used in other trades such as to provide strengthening to flimsy vacuum formed plastic products such as baths and shower trays. Spray lay-up presents increased fire hazards as the quantities of hazardous resins and catalyst required for spray lay-up are significantly more than in the hand lay-up process and the machinery requires a reservoir of resin and catalyst to be in close proximity.
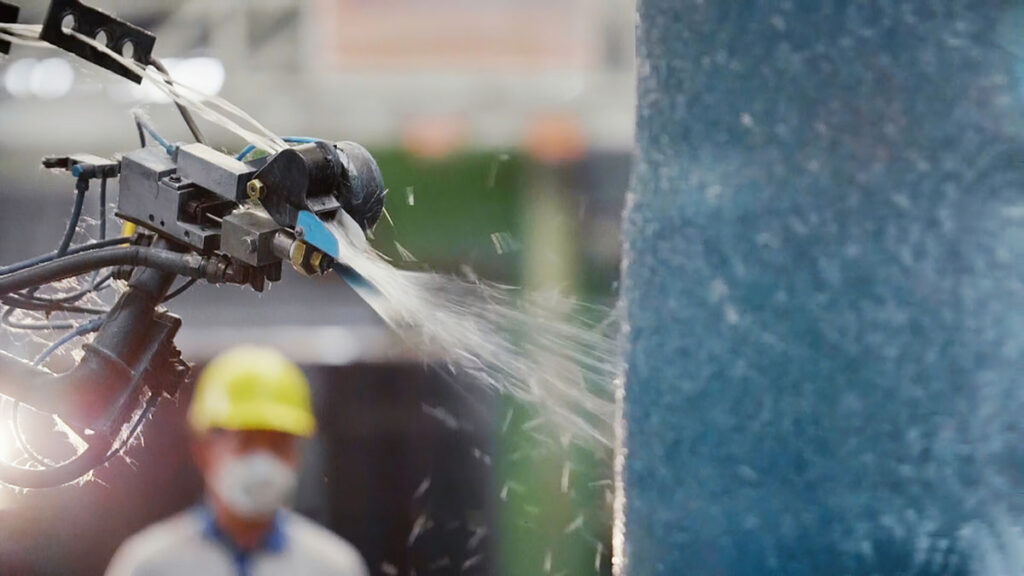
Fire/Explosion Hazards
- Catalysts often contain peroxides which burn vigorously with accelerant, such as the other products used in the GRP production process. A small fire can therefore get rapidly out of control and is difficult to fight.
- Resins and gel coats are flammable/highly flammable typically having a flashpoint of <40oC and therefore present a significant fire risk if not properly controlled.
- Modern resins are normally supplied ‘pre-accelerated’ to speed up the curing process, but if adding a chemical accelerator this is usually in a solvent carrier which is itself highly flammable.
- Acetone is used as a solvent cleaner for implements used in laying and is highly volatile with a flashpoint of -20oC and ignites easily.
- The moulding process is messy with splashes, overspray and spills of hazardous materials accumulating on floors which will readily propagate fire.
- Rags will often be soaked in solvent and used to wipe down moulds and for equipment cleaning, these remain highly flammable when disposed of and will rapidly propagate fire.
- Flammable vapours from the use and handling of the above-mentioned volatile chemicals in GRP workshops can reach concentrations that constitute a significant explosion risk.
- Dust released during trimming of mouldings is combustible. A ‘cloud’ of combustible dust can also cause an explosion if ignited.
Health and Safety
In addition to normal documentation/procedural expectations in terms of health and safety, GRP moulding presents a number of specific trade hazards.
Many of the chemicals used in GRP fabrication are hazardous substances that may cause injury or ill health to workers if they are not handled properly or no control measures are in place, this is in addition to the fire and explosion hazards and controls described above.
- Handling of glass fibre: Chemically inert, but contact can cause skin and eye irritation and inhalation may irritate the upper respiratory tract.
- Handling of resins: Polyester resin is usually dissolved in styrene with some containing up to 60% styrene, workers involved in laying up are often exposed to excessive amounts of styrene vapour during the application and curing stages with spray lay-up generating up to two to three times as much styrene vapour as the hand lay-up process.
- Short-term health effects of styrene: Mild to severe irritation of eyes, nose and throat and skin. Headaches, dizziness, fatigue, slowed reaction times, reduced dexterity.
- Long-term health effects of styrene: Repeated exposure can affect the central nervous system, possible carcinogen and evidence of chromosomal change in styrene exposed workers has been found.
- Handling of catalysts: Colourless liquid with a characteristic odour. Irritating and corrosive to eyes, nose, throat, airways and lungs. Irreversible damage to eyes can be caused by prolonged contact. Very toxic and corrosive presenting the risk of serious injury and ill-health.
- Cutting and sanding of GRP: Dust is created which can cause irritation to the skin, eyes and respiratory system.
- Cleaning solvents: Typically acetone vapour is irritating to the eyes and respiratory tract and can affect the central nervous system, liver and kidneys. Prolonged contact with the skin can cause dermatitis.
- Fillers and pigments: Mixed into resins for decoration and for technical enhancements to the product such as hardness, usually these are powders such as silica, calcium carbonate and some metals. These can cause a dust nuisance and depending on the powder, a substantial risk to the respiratory system.
- Hand-arm vibration syndrome: Exposure during cutting, sanding, trimming.
- Manual handling risk: Especially with larger GRP items.
- Slips and trips: Due to it being a messy trade with contamination of flooring inevitable, in addition to creating normal housekeeping issues.
Summary
GRP moulding presents a dangerous and potential toxic cocktail of trade risks for risk managers and an increased risk for insurers from both a Property and Liability perspective and should be managed accordingly.