Technical Talks is our series of risk management articles, produced by our in-house team of portfolio underwriting, risk managers and surveyors, offering support and guidance for you and your clients in relation to everyday business solutions.
Introduction
Fires in warehouses are a common occurrence, often resulting in large losses both in terms of Material Damage and Business Interruption.
Commercial demands have led to the construction of ever larger warehouse buildings, which are typically of lightweight construction with no internal fire compartmentation and where the cost-effective use of available space results in a very high fire load, with goods densely packed in narrow aisle, high bay racking systems.
The potential for rapid fire spread in these types of buildings may also present firefighting and life safety challenges, with Fire Brigade efforts likely to be limited to ‘dampening down’ from the outside to restrict the fire spreading to surrounding buildings.
The most common caused of fires in Warehouses are:
- Deliberate – Arson.
- Electrical faults.
- Lighting apparatus.
- Charges of Forklift Trucks.
- Flames, heat and sparks from hot works by Maintenance Operatives and Contractors.
- Use of shrink wrapping and heat-sealing equipment.
- Mechanical failure of conveyors and other machinery.
- Use of unsuitable Heaters.
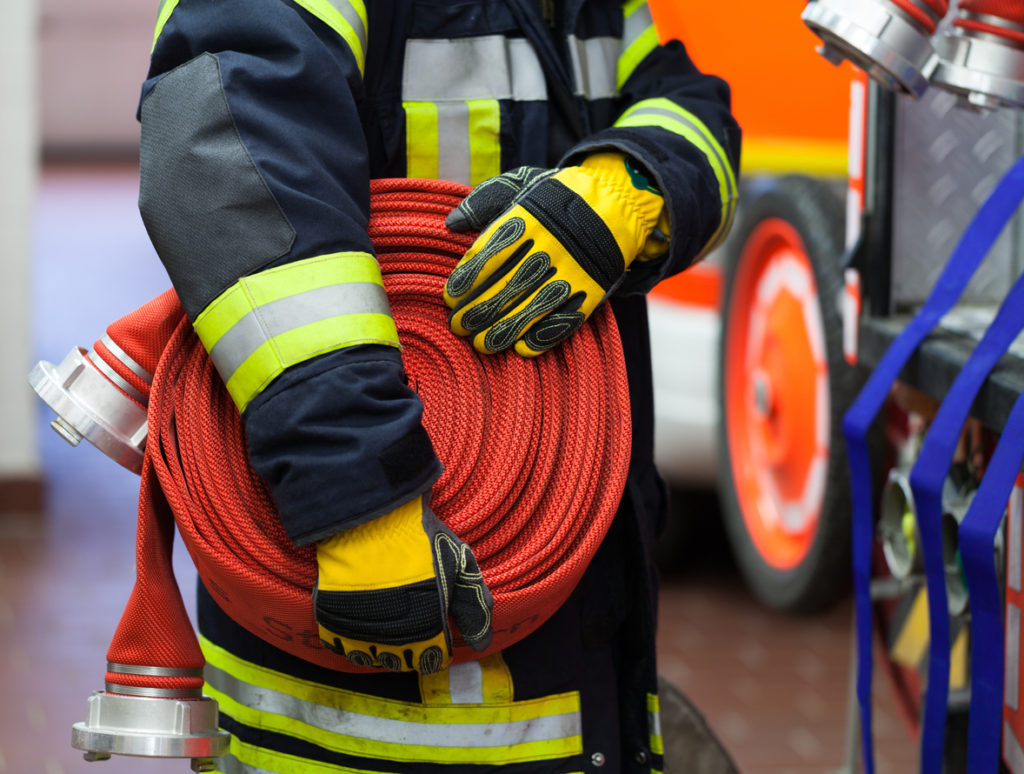
Risk Control Measures
Premises Security
The premises should be fully protected against intruders and malicious damage by the provision of security measures that are commensurate with the risk, such measures are likely to include a combination of the following:
- Perimeter fencing (ideally palisade fencing to 2.4 metres) and locked gates.
- Manned guarding.
- CCTV – ideally a remotely monitored event activated CCTV system conforming to BS8418. Designed, installed and maintained by a company that is ISO 9001 certificated and approved by a UKAS accredited inspectorate.
- Physical security to the building, such as appropriate locks to doors and windows, security shutters, window bars and grilles and antiram raid bollards.
- Installation of an intruder alarm by a company that is ISO 9001 certificated and approved by a UKAS accredited inspectorate. The system conforming with EN50131-1 in accordance with PD 6662 and with an alarm transmission system operating at performance level DP3 to an approved Alarm Receiving Centre (ARC).
Electrical
Electrical installations must be correctly designed, installed and maintained with inspection and testing at periodic intervals in accordance with BS7671:2018 “Requirements for Electrical Installations” undertaken by a qualified electrical contractor. Undertake portable appliance testing (PAT) as defined in the respective risk assessment.
Heating
Avoid all types of portable heater in favour of fixed heating systems, which should be professional maintained.
Housekeeping
- Keep goods a minimum of 0.5 metres clear of light fittings. Where high density discharge lighting is used, the manufacturer’s guidance relating to safe lamp clearance distances and the provision of lamp containment barriers should be observed. Irrespective of the type of lighting installation, luminaires should be positioned within aisles, rather than directly above stock.
- Keep electrical switchgear, heating equipment and other plant 1 metre clear of storage and provide guarding if required.
- Provide clearly defined storage arrangements interspaced with aisles of adequate width to facilitate full premises access / inspection and adequate means of escape.
- Hazardous materials such as flammable liquids, oxidising agents and aerosol products should be suitably segregated as determined by a site DSEAR (the Dangerous Substances and Explosive Atmospheres Regulations) risk assessment.
- Storage of waste skips, idle pallets and other combustibles outside the building should be minimised. Where unavoidable such storage should be as far as practically possible from the building or other property with a minimum distance of 5 metres expected.
- Waste materials should be removed from the building at the end of working day, or more frequently if necessary, and transferred to external metal bins or skips located as described above. Waste burning is to be prohibited.
- Smoking must be prohibited throughout the premises in accordance with smoke free legislation. Any external smoking enclosure should be of non combustible construction and suitably sited. No materials of a combustible or flammable nature should be located within 5 metres of the smoking shelter and suitable metal receptacles for discarded smoking materials must be provided.
- The number of gas cylinders stored for handling machinery fuel should be kept to a minimum and retained in a secure, well ventilated location away from potential sources of ignition and shaded from direct sunlight.
- Formal closedown procedures should be in place including inspections of all areas of the warehouse by a responsible person checking that any waste materials have been removed, that plant and services have been isolated as required and that all fire and security protection systems are operational.
- Where present, composite panels must be in good condition, with adequate management protocols in place please refer to a Risk Control Surveyor.
Trade Activities
- Forklift Truck charging should be undertaken in a designated well ventilated area with a clear space of at least 2 metres around the charging equipment and the truck undergoing charge.
- Hot working should be eliminated wherever possible. Where this is unavoidable, a competent person or contractor should be used and the fire hazard must be controlled by use of a formal Hot Work Permit system.
- Shrink wrapping should be undertaken by trained staff, in a suitable area of the premises clear of combustibles. Shrink wrapping equipment is to be used and maintained in accordance with the manufacturer’s instructions and suitable fire extinguishers kept in proximity. Shrink wrapping guns should be fitted with a ‘Dead Man’s Handle’ where required.
- Preventative maintenance of conveyors and other similar plant will reduce the production of friction heat and build up of static electricity.
Fire Safety Procedures
Establish fire safety procedures and train all staff in the actions to be taken in the event of a fire. Develop a self inspection programme to ensure that housekeeping rules are complied with that fire protection measures, equipment and procedures are fully functional.
Fire Protection
- Provide a suitable number and type of portable fire extinguishing appliances at appropriate locations throughout the premises and have them maintained under an annual service contract in accordance with BS53063 by a competent contractor. Engage a contract with a competent company to enable staff to effect 1st aid firefighting where it is appropriate and safe to do so.
- Installation of an automatic fire alarm system, conforming to BS5839: Part 1:2017. The system is to be designed, installed, commissioned and maintained by a competent contractor, who is either LPCB or BAFE approved. The system should provide dual path signalling to an approved alarm receiving centre.
- Consideration should be given to the installation of an automatic sprinkler system in accordance with the LPC Sprinkler Rules.
- Any new or existing sprinkler system needs to be properly tested and maintained to ensure that it remains fully operational at all times. Weekly testing must be carried out by a suitably trained person or contracted out to an LPCB approved company. A maintenance / service contract is to be in place with a contractor approved by the LPCB.
Goods within the warehouse
The goods stored within a warehouse have a huge impact upon the fire load. Anything explosive or flammable is often carefully regulated. The hazards of soft furnishings, aerosols, paper products etc are well known.
However, lithium-ion batteries have caused some significant fires in the warehousing sector and the intensity and difficulty to extinguish is impacting the insurance and reinsurance markets. They are found in many products and can include: renewable energy and solar panels; electric bikes and scooters; phones; tablets; laptops; vaping devices; portable electric hand tools; electric toothbrushes; cordless electric household and garden equipment etc. The research and development that goes into the battery technology within the big blue chip consumer product manufacturers is reassuring and thankfully failures are rare. However, failure rate is much higher with cheaper imported lithium battery powered products of unknown provenance and cheaper replacement batteries for e bikes and scooters.
- In 2021, a fire involving lithium‑ion batteries occurred in the U.S. which took firefighters two weeks to completely extinguish. Batteries for telecommunications systems, renewable energy, utilities, and emergency lighting systems were stored in the warehouse.
- In January 2023, a fire occurred in a French warehouse complex with three storage units of approximately 6,000 m² each. The fire started in a unit that stored 12,500 lithium‑ion batteries for cars. It spread to the other units and took 137 firefighters with 60 fire engines to extinguish the blaze.
- The fire at a modern robot-operated distribution warehouse for a UK online grocery retailer caused concern when one of the robots, equipped with lithium‑ion batteries, started to burn and set fire to other vehicles and to the warehouse. Ultimately, 200 firefighters were needed to extinguish the blaze and the warehouse was a total loss
Knowing not only the nature, but also the provenance of goods stored is becoming much more important.
For more information, please contact your local branch.
Note: Information detailed in Technical Talks has not been verified for accuracy by a third party. None of the information should be taken as legal or professional advice.