Technical Talks is our series of risk management articles, produced by our in-house team of portfolio underwriting, risk managers and surveyors, offering support and guidance for you and your clients in relation to everyday business solutions.
Introduction
Using wood instead of fossil fuels is seen as a greener option, and wood chips and pellets were already cheaper than gas, heating oil and electricity even before the recent energy price rises. It’s little wonder biomass boilers are becoming increasingly popular.
Biomass boilers (not to be confused with waste wood burners commonly found in woodworking trades) are designed to operate unattended 24 hours a day with periodic, scheduled maintenance.
However, they do pose additional fire hazards as outlined in our Technical Talk. Our Risk Control Managers are also happy to provide risk management guidance to policyholders thinking about biomass boilers.
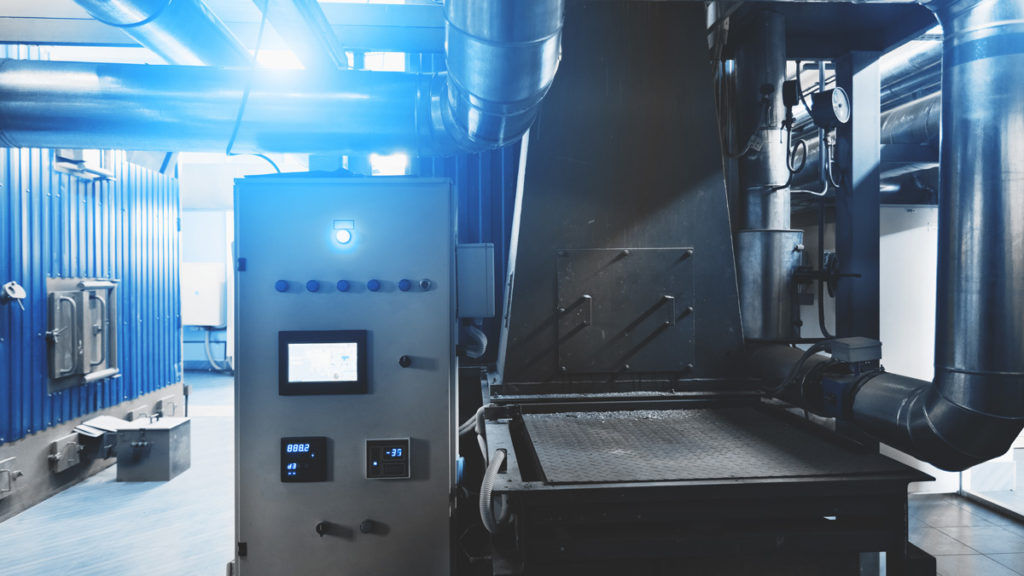
Key Features of a Biomass Boiler
- Biomass boilers are designed to operate unattended 24 hours a day with periodic, scheduled maintenance.
- Generally fed by pellets or wood chips which are bought in, stored in bulk fuel containers or hoppers with automatic fuel delivery systems to the burners — normally auger feeds.
- Some businesses may chip their own waste wood to be used as fuel.
- Heating is generally provided through heat exchanges to hot water or hot air-based heating systems.
- New technology but becoming widely established.
- Requires installation and maintenance by a competent company/person.
Industry Standards
Biomass systems already have an established market share, but with this being relatively new technology, there are limited industry accreditations and no formal UK/EN standards for Biomass Boilers, their manufacturers, installation or maintenance companies. It is therefore important the quality and safety of the product and installation can be established via trade and manufacturer’s websites. The following should be considered in any such assessment:
- Product accreditation to independent or national standards (Scandinavia and Germany where Biomass is a more established technology have national standards).
- Design and installation in accordance with the manufacturer’s recommendations by suitably trained and qualified persons.
- The boiler, flue and all safety devices must be inspected, cleaned, serviced and maintained in accordance with the manufacture’s recommended schedules or at least annually by a suitably trained and qualified person. In the absence of any formal accreditation body/standard for installers, information must be ascertained regarding the installers expertise and should consider:
- Their experience/number of similar installations completed.
- Completion by engineers/designers of manufacturer’s training courses.
- Qualifications/memberships such HETAS, Microgeneration Certification Scheme.
Hazards to Watch
- Burn back — with heaters generally automatically fed, the potential exists for so called burn-back where fire in the combustion chamber of the heater travels back through the fuel delivery system to ignite the stored fuel reserves.
- Equipment failure — the introduction of a combustion-based heating system to any site increases the potential for a fire incident through equipment failure, poor installation, inadequate maintenance or improper use.
- Housekeeping — wood pellets, shavings and wood waste can collect near boilers, electrics, and fuel storage areas. Also, Biomass boiler rooms are often used for general storage. This can significantly increase the risk of fire inception.
- Fuel Storage — bulk storage of readily combustible biomass fuels introduces additional fire load and resultant increased fire safety hazards to a site. Fuel that is delivered with too high a moisture content (30% plus), or stored in an area where it can absorb moisture can, in extreme cases, spontaneously combust.
- Fuel Transport — fuel delivery systems can create an increased risk of dust explosion during filling of silos and hoppers.
- Flue fires — flues can become extremely hot and can ignite combustible elements of construction or other combustibles where they are positioned too close or in contact.
- Un-combusted gas — can build up following flame failure and can create an explosion risk if restarting is not undertaken correctly.
- Operator error — improper start-up/restart or failure to follow safe operating procedures by the user can increase the risk of fire or explosion.
- Unattended running — these heaters will continue to burn whilst the premises are closed reducing the opportunity for early detection and subsequent emergency action should a fire break out.
- Ash removal — excessive ash build up can spill over to inappropriate areas or effect proper operation of boiler.
Control Measures to Tackle Risks
The following loss control measures should be considered where a Biomass system is in use or proposed:
Burn Back Protection
The automatic in-feed auger (also known as stoker auger) fuel delivery system must have burn back protection, including a mechanical fire stopping device between the burner and the fuel store such as a rotary valve or an airtight shutter/burn back flap AND an automatic water dousing system in the feed auger linked to a heat detection device in the conveyor housing. (Note under 50KW output systems may not be suitable to have burn back protection installed, these often feature hand/gravity fed hoppers built into the device.)
Control Equipment/Shut Off Devices
Modern boilers will normally have an automatic control system providing a lock out/shut down feature which will require manual reset in the event of a number of potential circumstances. These include overheating, build-up of uncombusted gas in the burner/flue, build-up of carbon monoxide in the plant room or opening of the combustion chamber door. Jam switches should be fitted on all augers.
Installation, Cleaning and Maintenance by a Competent Person
The boiler, flue and all safety devices must be inspected, cleaned, serviced, and maintained in accordance with the manufacture’s recommended schedules or at least annually by a suitably trained and qualified person. Insulated flues should be used and a clear space of at least 1m maintained from combustible materials. Where the heater flue passes through a floor, ceiling, wall or partition that contains combustible materials a 50mm air gap (150mm for a single wall flue) around the flue or a proprietary fire-resisting sleeve or collar should be fitted. Spark arrestors to flues are not recommended as they can cause soot build up.
Separation/Compartmentation
Ideally the biomass boiler and associated fuel store should be located in an external building of non-combustible construction or purpose built structure separate from the main property by at least 10 metres or as far as is reasonably practical. Where located inside a building the plant and fuel store should preferably be located in a dedicated plant room with 1 hour fire separation, if not a clear space of at least 3 metres will be required around the plant and associated equipment. Provision of automatic Fire Alarm detection in the area of the installation with offsite signalling is preferred.
Staff Training
Operation of the system to be in accordance with the manufacturer’s instructions by staff who have undergone operational, routine maintenance and emergency procedures training. Start-up and restart training to be included as it is important the correct safety checks and procedures are followed.
Housekeeping
Boiler room/compartment should be kept clear of combustible materials. Any spilled pellets, wood chip or overfill in the boiler compartment should be cleared promptly and the compartment inspected at least weekly. All waste ash is to be collected and retained within a proprietary metal lidded receptacle – preferably located externally and fed by screw mechanism incorporating fire dampers to any wall openings. These can be fitted with interlock switches to shut down the boiler if they become detached or full during operation.
Fuel/Pellet Storage
The correct storage arrangements for pellets or woodchip is essential to prevent moisture absorption and the resultant risk of spontaneous combustion. Only fuels recommended by the manufacturer and from reliable sources (to avoid contamination and guarantee moisture content) are to be used in the boiler and be within specification for moisture content. The European Union has developed specifications and standards — CEN/TC 335 for solid biofuels. If chipping own fuel, procedures are required to ensure the appropriate moisture content requirements are adhered to. Electrical fittings should not be present in fuel stores unless of an explosion proof type and an earthing point is
normally required for fuel delivery.
Health and Safety Considerations
Fire and Explosion Risks
A Fire Risk Assessment and, if necessary, a Dangerous Substances and Explosive Atmosphere Regulations (DSEAR) assessment should be undertaken, or existing documentation reviewed and updated to ensure suitability.
Carbon Monoxide
There is a risk that wood pellets in enclosed stores can produce carbon monoxide. Storage areas should be treated as confined spaces and appropriate ventilation and gas checks to be undertaken before entering enclosed stores or hoppers. Access doors should be locked, and signage posted advising that entry is subject to a Permit to Work.
For more information, please contact your local branch.
Note: Information detailed in Technical Talks has not been verified for accuracy by a third party. None of the information should be taken as legal or professional advice.