Technical Talks is our series of risk management articles, produced by our in-house team of portfolio underwriting, risk managers and surveyors, offering support and guidance for you and your clients in relation to everyday business solutions.
General
Effective housekeeping can eliminate or reduce workplace hazards and is a key feature of accident and fire prevention. It also improves the general working environment and efficiency and so brings other benefits to a business.
Housekeeping is not just cleanliness. It includes keeping work areas neat and orderly, maintaining floors free of slip and trip hazards, managing waste, and developing suitable procedures for using and storing trade materials. Housekeeping provides a good indicator of the quality and attitude of management at a business.
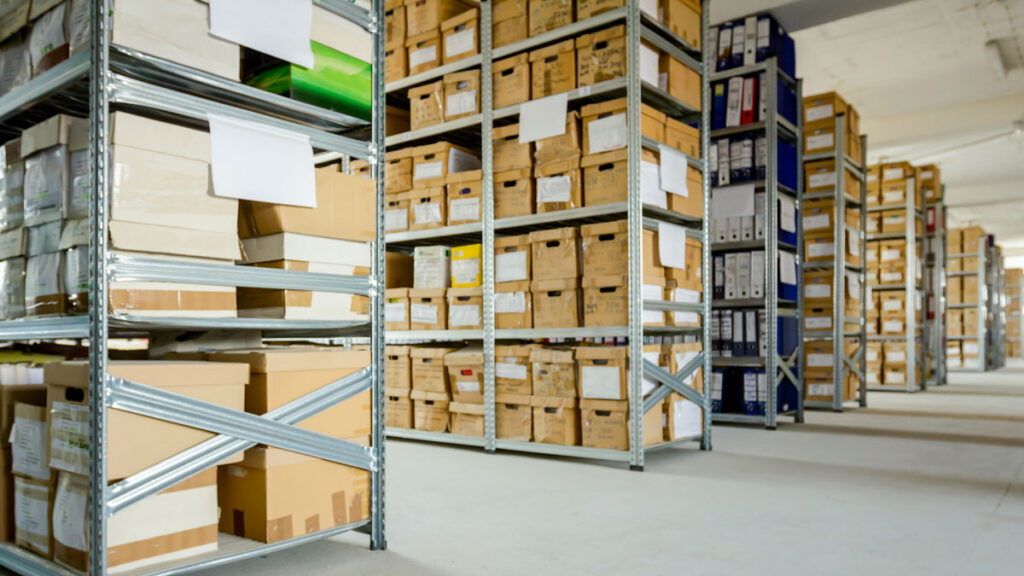
The following should be considered as minimum operational standards for all premises:
- Premises (including buildings, yards, and parking areas) should be kept clean, tidy, and organised, allowing for unhindered movement of personnel and vehicles.
- Procedures should be in place to clean and remove combustible trade waste from work areas at least daily. Waste should be stored in a designated, preferably secure area whilst awaiting disposal, and removed from the premises at least weekly.
- Suitable regimes should be in place for maintenance and cleaning of plant/equipment specific to the processes and activities undertaken e.g. periodic cleaning of grease extraction filters and ducting in restaurants.
- Oily or impregnated rags / wipes should be stored in metal containers with metal lids, until removed from the premises, to minimise the risk of fire by spontaneous combustion.
- Mineral absorbent granules or proprietary spill kits should be used, rather than sawdust, to soak up oil leaks or similar spillages.
- All sawdust, shavings and other trade waste should be cleared (particularly around electrical motors and machinery), bagged and removed from the buildings at the end of each working day. All overhead light fittings, service trunking and roof supports should be cleared of dust and fly accumulations. An industrial vacuum should be used instead of redistributing dust with a broom.
- Paper waste should be swept up daily, bagged or baled and removed from the premises at least weekly.
- Waste burning on site must be prohibited to prevent the risk of accidental ignition of combustible materials by floating embers.
- Smoking must be prohibited within buildings in accordance with current Regulations. Designated smoking areas / shelters should be provided in the open, which should be sited clear of any combustible materials, storage facilities for combustibles, flammables, or structures of combustible construction. Facilities for the safe disposal of waste smoking materials should be provided, such as proprietary metal receptacles, or metal bins part filled with sand.
- Suitable controls must be implemented for use and storage of flammable liquids or gases, following regulatory or trade guidance, for example:
- All flammable liquids with a flash point below 32oC and stored within the premises should be kept within a fire-resistant metal cupboard or metal bin with a metal lid. The total quantity of any such flammables must not exceed 50 litres. For storage over 50 litres, a purpose-built store must be used – please refer to a Risk Control Surveyor for guidance.
- The number of spare gas cylinders should be kept to a minimum, with storage either in a detached building of non- combustible construction or, in the open within a secure cage or fenced compound away from potential ignition sources, with good ventilation and shaded from direct sunlight.
Oxygen cylinders should be stored at least 3 metres away from flammable gas cylinders.
Storage
Storage of combustible goods and materials, common to many trades and occupancies, present a fire hazard, and must be managed properly. In order to minimise the risk of combustible materials coming into contact with sources of ignition and resultant fire, the following storage practices should be adopted:
- A clearance of at least one metre should be maintained from heating appliances and electrical switchgear – designated by fencing/barriers of non-combustible construction or clear floor markings.
- Clearance of at least 0.5 metres should be maintained from electrical light fittings.
- Clearance of at least 2 metres should be maintained from forklift battery charging equipment – again with suitable demarcation / signage.
- All external storage, including idle pallets, should be situated at least 5 metres clear of the buildings.
- Freestanding storage or within racking should be safely stacked in an orderly manner to minimise the risk of contact with ignition sources.
From a fire safety perspective, fire exit aisles and doors must always be kept clear to ensure safe egress from the premises.