Technical Talks is our series of risk management articles, produced by our in-house team of portfolio underwriting, risk managers and surveyors, offering support and guidance for you and your clients in relation to everyday business solutions.
Introduction
Deliveries and collections are essential to business but can be some of the most dangerous activities to deal with. Every year, about 70 people are killed and thousands suffer major injuries in accidents involving vehicles in and around workplaces and many result in criminal prosecutions. A significant number of these occur during deliveries and collections. Unless effective precautions are taken, people are at risk from:
- being hit by moving vehicles.
- falling from vehicles.
- vehicles turning over.
- being hit by objects falling from vehicles.
- slips and trips in the general work area and on or from the vehicle.
- handling injuries when moving the goods.
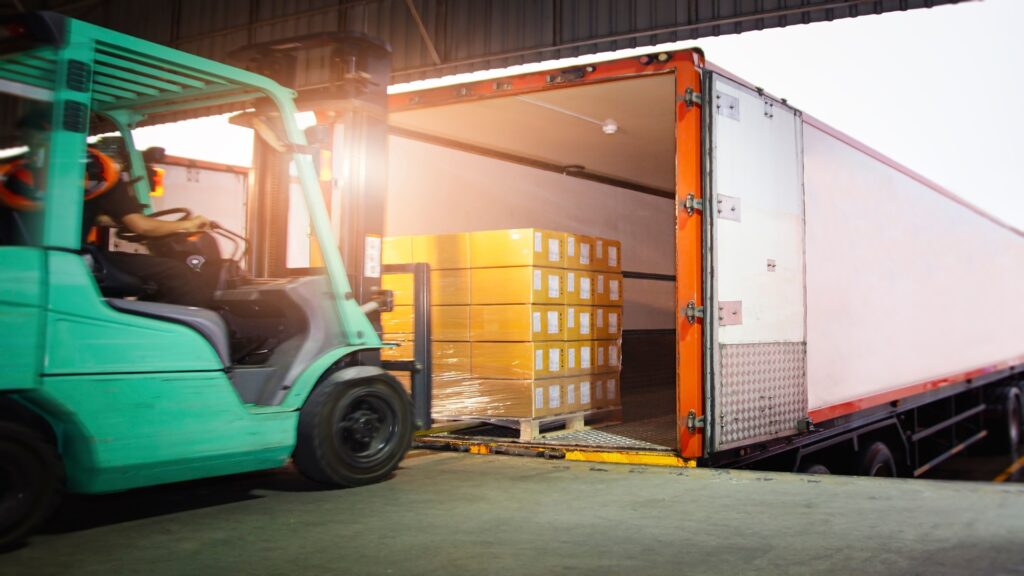
Loading and Unloading Methods
The most commonly found loading and unloading methods are as follows:
Forklift Vehicles
Forklift vehicles can include tele-handlers, Side Loaders as well as the most commonly found Counterbalance Forklift Truck. These are ride-on, driver-operated vehicles. There are also smaller, powered “Pallet Trucks” which the operator will control whilst walking behind the unit or standing on a small, attached platform. Normally used for loading/unloading palletised goods but can also be used for some stable non-palletised items. They are extremely widespread and wide-ranging use and commonly found in warehousing, timber merchants and multiple types of workshops.
Lorry Mounted Crane
This is often referred to by the brand name Hiab, but there are other brands such as Palfinger. This is a vehicle with an attached, self-powered, hydraulically operated crane. Typically used by businesses delivering building materials, to anywhere from a private house to a large construction site but can have many other applications.
Crane
Can be permanent fixed cranes such as Jib Cranes or Overhead Travelling Cranes within workshops; shipping and handling cranes at goods yards, transport and transit depots and the like; as well as temporary tower cranes such as those found on construction sites. The customer or site responsible for the crane should arrange for trained operators, and where appropriate, signallers and banksmen. On some occasions a documented lifting plan may also be required.
Tail Lift
A tail lift is a mechanical device permanently installed on the rear of a work truck, van or lorry and is designed to enable the loading/unloading of goods from ground level or a loading dock to the level of the vehicle bed, or vice versa. Extensively used for delivery to retail premises where unloading of goods in cages or trolleys can occur at the roadside, in car parks and yards, etc.
Manual Handling
Manual handling involves one or more employees manually lifting, putting down, pushing, pulling, carrying or moving a load, and is commonly linked to back injury. Although, most typically seen in the courier (parcels and packages) and retail (such as delivery of furniture and white electrical goods) sectors, loading and unloading using manual handling remains extremely wide spread and can include a very wide range of trades.
Responsibility
The safety of everyone at premises, including people visiting the site, is the responsibility of the organisation in charge of the site, as they should control what takes place there.
However, there can often be three different employers involved in activities involving loading and unloading at an individual premises and these could each be classed as Duty Holders to some degree, depending on the tasks. These key Duty Holders are:
- the supplier, sending the goods.
- the carrier — the haulier or other company carrying the goods; and
- the recipient — the person receiving the goods.
Whilst not a legal requirement, an agreement on who is responsible for what in terms of safety can be very important. Ideally, this should be agreed between all parties and where appropriate include a “safe delivery plan”.
Legal Obligations
The Health & Safety at Work etc. Act 1974 requires Employers to ensure the health, safety and welfare of employees and others in the workplace, so far as is reasonably practicable. This duty extends to the requirement for suitable and sufficient assessment of risks, provision and maintenance of safe systems of work and provision of any necessary information, instruction, training and supervision.
Once responsibilities have been decided between the Duty Holders, and to then ensure they comply with their legal duties, employers should ensure they: –
- Undertake formal Risk Assessment in respect of loading and unloading operations.
- Implement a written Safe System of Work (SSOW) based on Risk Assessment.
- Communicate the SSOW to drivers, including external and agency personnel, who should acknowledge by signature, and ensure proper communication to drivers whose first language may not be English.
- Monitor to ensure ongoing compliance with the safe system of work.
- Review the risk assessment and SSOW to ensure these remain appropriate.
A clear and unambiguous Safe System of Work (SSOW) for unloading vehicles should detail the necessary instructions, equipment and co-operation for unloading vehicles safely. The following information provides some detail on accepted good practice for loading and unloading activities and would be typical of the information included in a SSOW and Driver training and instruction.
Loading Location
Loading and unloading areas should:
- Be clear of other traffic, pedestrians and people not involved in loading or unloading.
- Be clear of overhead cables, pipes, or other dangerous obstructions.
- Be on firm level ground.
- Have a safe place for drivers to wait (not in cab unless a necessity).
- Be provided with fence/edge protection or other fall arrest system where there is a danger of people falling.
- If necessary, be protected against bad weather, e.g. strong winds can be very dangerous during loading.
Those off-loading may face unexpected or unusual situations during their work:
- They should be trained to identify acceptable loading/unloading arrangements.
- Checklists can help to check that reasonable precautions are in place.
- Agency drivers should be made familiar with arrangements for delivery safety.
- Those involved in off-loading should be given authority to refuse loading/unloading of a vehicle on safety grounds.
Load Features
Uneven loads can make the vehicle or trailer unstable, and improperly loaded or secured loads can move around in transit making unloading extremely dangerous.
- Loads should be spread as evenly as possible and secured in place if possible.
- Heavy loads are dangerous; thought is needed as to how they can be controlled.
- Vehicles must not be overloaded; this can cause difficulty in steering or braking.
- Dock levellers or tail lifts should have guards or skirting plates.
- Vehicle and trailer must be stable for loading — brakes engaged; trailer stabilised.
Other Precautions Which May Be Required
- Load in such a way as to make the unloading sequence logical and safe.
- Before unloading, check that loads have not shifted during transit.
- Ensure that competent people are in charge of loading/unloading. For complex loads this may require banksmen, signallers and a lifting plan.
- Hauliers and recipients should exchange details in advance if loads are difficult to secure in a safe manner.
- Safeguards to stop drivers accidentally driving away too early. Could include:
- traffic lights
- the use of vehicle or trailer restraints
- person in charge of loading holds vehicle keys/paperwork until safe to move.
(These safeguards would be especially effective where communication problems could arise, e.g. where drivers do not have English as their first language.)
- Ensure personnel are protected from moving mechanical parts such as dock levellers or tail lifts.
- Automated load sheeting systems can be fitted which do not require employees to climb on loads or trailers to apply protective sheeting. If this is not possible, then an appropriate fall arrest system should be used.
Note: Information detailed in Technical Talks has not been verified for accuracy by a third party. None of the information should be taken as legal or professional advice.