If businesses are looking to achieve the highest standards of health and safety guidelines at work, then applying a methodology such as the ‘hierarchy of controls’ can prove useful.
The ‘hierarchy of controls’ ensures a consistent approach for businesses managing safety in the workplace. It provides a structure to select the most effective control measures to eliminate or reduce the identified risks or hazards.
Risks should be reduced to the lowest reasonably practicable level by applying control measures, in the form of a risk management process, by order of priority. This is what is meant by a hierarchy of control. While many versions exist, below is the methodology that Arch Business Protection (BCarm) suggests.
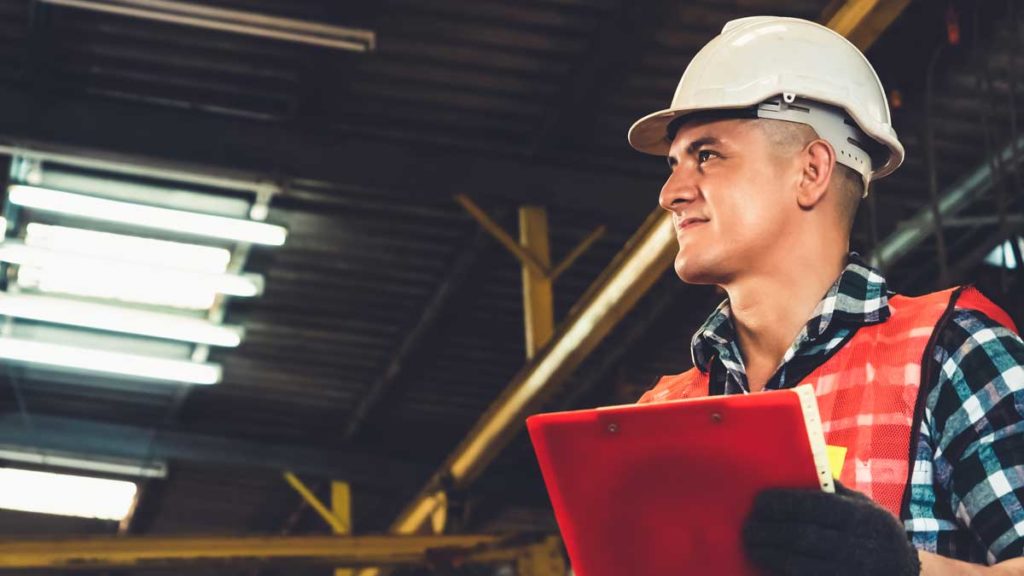
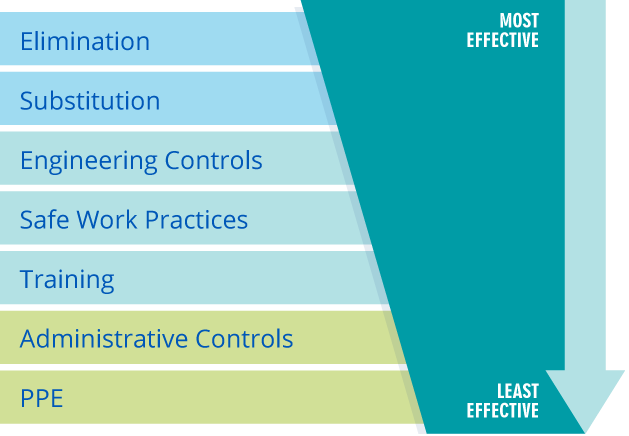
The full structure of the hierarchy of controls includes:
Elimination
Elimination is the most effective way to control a risk because the hazard is no longer present and should be the preferential way to control a hazard. An example could be removing a working-at-height risk by conducting the work at ground level or eliminating hazardous machinery that can cause harm to users.
Substitution
If not reasonably practicable to eliminate the hazards and risks, businesses must minimise the risks using the substitution method, e.g., replacing the task with a less risky way to achieve the same outcome.
Engineering Controls
This is a physical control measure that controls the hazard at its source (requires a physical change at the workplace). For instance, placing guards around moving parts of machinery, or installing sound dampening measures to reduce exposure to unpleasant or hazardous noise.
Safe Work Practice(s)
Safe Work Practices will include work methods to minimise exposure and provide training and instruction needed to ensure workers can work safely. Businesses should develop safe working procedures that aim to describe the task, identify the hazards and document how the tasks are to be performed to achieve minimal risk.
Training
Workers should be trained to develop skills and knowledge of the risks they are exposed to, and support managers in identifying and managing health and safety risks. They must then be able to demonstrate that they are competent in performing the task according to the procedure; this could be in the form of a test.
Administrative Control(s)
By adopting alternative work practices to protect workers from hazards, such as limiting exposure time to a hazardous task, e.g. a noisy area for and/or use signs to warn people of a hazard.
Personal Protective Equipment (PPE)
The final control step is to provide PPE to staff. PPE includes everything from safety glasses, to hardhats, to fire-retardant clothing, ear defenders and safety boots. Some industries will also require warning devices that are worn by the user, such as gas detectors. Ensure all PPE passes the following checklist:
- Specification — is it suitable for the given task?
- Fitting — items such as dust masks will often require specialist fitting to ensure an adequate seal.
- Training in use — staff wearing PPE require the correct training, it is important they understand the reason for use.
If more than one item of PPE is to be worn, they must be compatible with each other and when used together, should adequately control the risks.
Putting It into Practice
Each level of control will have its intricacies dependent on the industry. The hierarchy of controls is a simple way for businesses to look at how to assess and prioritise control measures, to ensure the most effective steps to protect staff are taken. These controls should be reviewed on a regular basis to ensure they remain adequate and continue to be followed in order to provide a safer and more productive workplace.
Source: Arch Business Protection