Technical Talks is our series of risk management articles, produced by our in-house team of portfolio underwriting, risk managers and surveyors, offering support and guidance for you and your clients in relation to everyday business solutions.
Introduction
Gradually operating disease exposures are a significant concern to Insurers as many can result in permanent, life changing conditions, which develop due to exposure over an extended time period. However, it should be noted that whilst some conditions can take many years to develop, concentrated exposure to the causes of certain conditions can result in a more rapid onset.
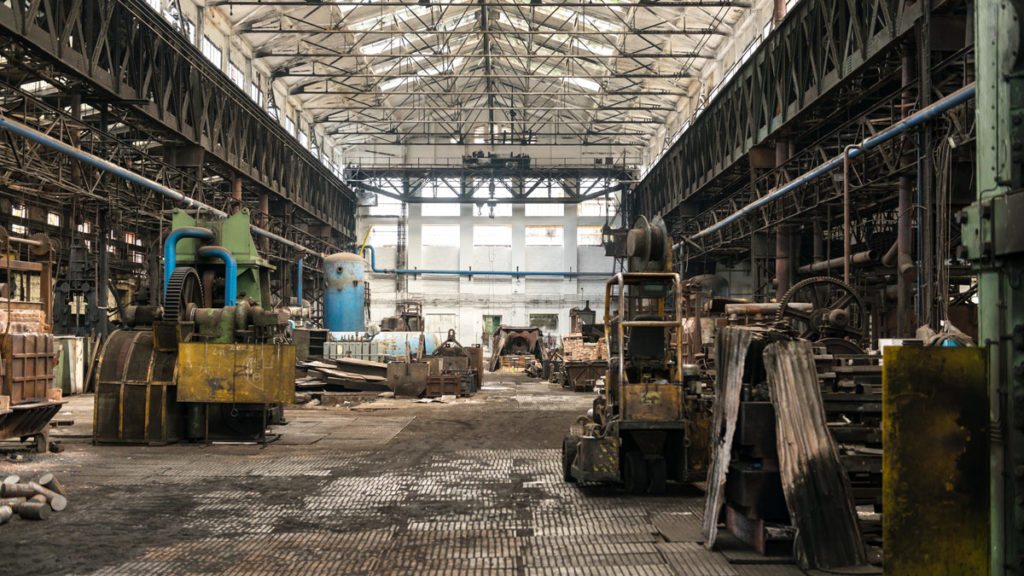
Hazardous Substances
Hazardous substances can take many forms and can include:
- Chemicals.
- Products containing chemicals.
- Dusts.
- Vapours.
- Fumes.
- Mists.
- Gases and asphyxiating gases.
- Nanotechnology.
- Biological agents (germs).
- Germs that causes diseases (e.g. leptospirosis/legionnaires and germs used in laboratories).
Legislation
All employers have a common law duty of care to ensure their employees’ health and safety at work. This duty is reinforced under a range of different legislation which is listed below:
- Health and Safety at Work etc Act (HASAWA) 1974.
- Management of Health and Safety at Work Regulations (MHSWR) 1999.
- Control of Substances Hazardous to Health Regulations (COSHH) 2002, as amended.
COSHH is the primary legislation that requires employers to control substances hazardous to health. COSHH sets out requirements for a wide range of substances and reparations (mixtures of two or more substances), including carcinogens, mutagens, asthmagens and biological agents, which have the potential to cause harm to health if they are ingested, inhaled, or are absorbed by, or come into contact with the skin, or other body membranes (e.g. eyes). The objective of COSHH is to prevent, or to adequately control, exposure to substances hazardous to health, to prevent ill health. COSHH establishes a system of Workplace Exposure Limits (WELs) and Biological Monitoring Guidance Values (BMGV). Any hazardous substances of any significance will be subject to a WELs/BMGVs. Such limits should be stated on the safety data sheet (SDS) or addressed in Guidance Note EH40 which is available on the HSE website.
An employer has an “absolute” duty to assess the risk to employees and all others affected by exposure to substances hazardous to health. SDS provides information on the chemical products (e.g. chemical classification, hazards, handling and storage arrangements, emergency measures etc.), which will assist with the users of the chemicals to complete a risk assessment. COSHH does not cover lead, asbestos or radioactive substances as these have their own specific regulations.
Effects
- Local — Causes harm at the point of first contact with the body.
- Systemic — Causes harm elsewhere than its point of first contact with the body (e.g. carbon monoxide is inhaled it has no direct effect on the lungs, however, it acts as a systemic poison by replacing oxygen in the bloodstream thereby affecting the cellular respiration).
Main Routes of Entry into the Body and Some Examples
- Eyes via absorption by the mucous membrane (conjunctiva) and then can gain route into the body through blood capillaries.
- Ears.
- Nose and mouth by inhalation.
- Hard/soft wood dusts during woodworking activities (e.g. sawing, cutting, routing, turning, sanding etc.) and when handling the cut timbers.
- Paint vapours, welding fumes and grinding dusts in engineering workshops and various other trades.
- Dusts and fibres in textiles and general manufacturing.
- Mouth by ingestion via digestive tract.
- Smoking, eating and drinking with contaminated hands/face.
- Skin via absorption through intact skin or though cuts/abrasions leading to occupational dermatitis and sensitisation or it can be transferred by the blood to target organ(s) or system(s).
- Working with oils, lubricants, degreasing agents and other chemicals (e.g. acids) in engineering workshops, motor traders etc.
- Working with dusts such as flours and other similar compounds.
- Adverse reactions to latex.
- Solvents such as Toluene and Trichloroethylene (referred to as Trike) can have local effect on the contact point and/or pass through into the bloodstream and target organ(s) or system(s).
- Skin via injection when something sharp, normally associated with needles (but can be broken glass, metal/wood splinters), can push through the external layer of skin and resulting in the hazardous substance entering the bloodstream and being carried around the body.
- Inhalation is the most significant route of entry for harmful substances, estimated to be around 90% of industrial poisons are absorbed through the lungs.
Common Signs and Symptoms of Workplace Harm to Health
- Lungs — wheezing, shortness of breath, coughing (possible with presence of blood) and allergic asthma with resultant, often permanent reduction in lung functionality.
- Skin — reddening of the skin, cracking blisters, dermatitis.
- Nose and eyes — increased mucus, swelling and reddening, often acute effect on contact.
- Digestive tract — nausea and vomiting, resulting from ingestion of a substance.
Risk Factors
As Insurers, we would expect an employer to be able to demonstrate adequate awareness, control and management of the risks arising from the presence of hazardous substances in their workplace.
The following are the risk factors which should be part of an effective COSHH risk assessment process:
- Hazardous properties of the substance (obtained from the SDS).
- Level of exposure to the substance(s) (e.g. amount and concentration of the substance).
Nature of the Task/Work Activity
- Number of people exposed (e.g. segregation/separation).
- Type of exposure (e.g. vapour/mist based on activity such as spraying compared to application by brushing).
- Duration and frequency of exposure.
- Controls.
- Morphology (e.g. how the substance may change in the process, such as mixed/heated).
- Effects of mixtures.
Control Measures
After evaluating the risk and taking into consideration the existing controls, additional measures may need to be introduced to ensure that the risks are being adequately controlled. A common hierarchy of control is detailed below:
- Elimination of the substance or work practice/activity.
- Reduce the use or frequency or substitute the substance for a lesser hazardous type (e.g. Trike very rarely used any longer as a degreasing agent) or change the physical form (e.g. pellets instead of dusts) or process/ways of working (e.g. automation or use of brush instead of spray).
- Isolation using enclosures/safety cabinets (e.g. fume cabinets/glove boxes/barrier isolators) for handling hazardous substances, enabling people to be isolated (or worker numbers reduced in the hazardous area) from the harmful substances.
- Control at source through engineering controls such as enclosures (e.g. containment to prevent free movement within the work environment) and the use of local exhaust ventilation (LEV)/extraction systems for fumes/dusts. LEV systems must be thoroughly tested and inspected by a competent person to ensure the systems are functioning correctly. Worker behaviour is an important aspect, specifically around compliance with control measures.
- Provision of personal and/or atmospheric exposure monitoring where appropriate.
- Personal Protective Equipment (PPE) which will provide a physical barrier between the individual worker and the risk. PPE includes overalls, gloves (can include gauntlets/full arm sleeves), eye protection, respirators or breathing apparatus, and must be suitable for the purpose, adequate (including face fit testing) and issued on a signed receipt basis. Furthermore, all non-disposable equipment, such as powered respirators/breathing apparatus should be maintained per manufacturer’s recommendations, with records of any inspections/maintenance carried out retained.
- Discipline such as rules, signs and instructions.
The application of the hierarchy encourages the use of the highest level of control for those risks with the highest rating. Only when it is found that it is not possible to use this control should the next highest control be used. A combination of the above measures is often used to control/manage a risk adequately.
PPE should be treated as a “last resort” if control of the exposure is not practicable by any other means. PPE does not eliminate the hazard and protects the user only and not the rest of the workforce. In addition, if the PPE fails, the employee will be exposed to the hazardous substances.
Monitoring and Health Surveillance
The results of relevant exposure monitoring and health surveillance will provide information on the effectiveness of the controls. If employees are being exposed to higher than intended levels of substances this can provide an indication of actual risk to their health and indicate areas where controls are not effective.
Monitoring is required to show compliance with the WELs or BMGV and confirm that the control measures are effective. Typical monitoring could be air quality monitoring/sampling, personal monitoring and biological monitoring.
The risk assessment should be used to identify if there is a need for Health Surveillance. Health surveillance can provide information on actual harm to health and illustrate that there may be a higher level of risk than was expected, it can also help identify groups of people particularly at risk (individual susceptibility).
Typical health surveillance must be carried out periodically by competent persons/medical practitioners and can include:
- Lung function/spirometry.
- Biological (e.g. blood/urine analysis) testing.
- Skin checks.
For more information, please contact your local branch.
Note: Information detailed in Technical Talks has not been verified for accuracy by a third party. None of the information should be taken as legal or professional advice.